Impact-Echo is a method for nondestructive evaluation of concrete and masonry, based on the use of impact-generated stress (sound) waves that propagate through the structure and are reflected by internal flaws and external surfaces. Impact-Echo can be used to make accurate, nondestructive, measurements of thickness in concrete slabs and plates, following an ASTM Standard. For details of the ASTM Standard, see
ASTM Designation C 1383-98a
The Annual Book of ASTM Standards(Copyright ASTM)AMERICAN SOCIETY FOR TESTING AND MATERIALS
100 Bar Harbor Dr., West Conshohoken, PA 19428
Impact-Echo can also be used to determine the location and extent of flaws such as cracks, delaminations, voids, honeycombing and debonding in plain, reinforced and post-tensioned concrete structures. It can locate voids in the subgrade directly beneath slabs and pavements, measure the depth of surface-opening cracks, and determine thickness or locate cracks, voids and other defects in masonry structures where the brick or block units are bonded together with mortar. Impact-echo is not adversely affected by the presence of steel reinforcing bars.
How Impact Echo Works
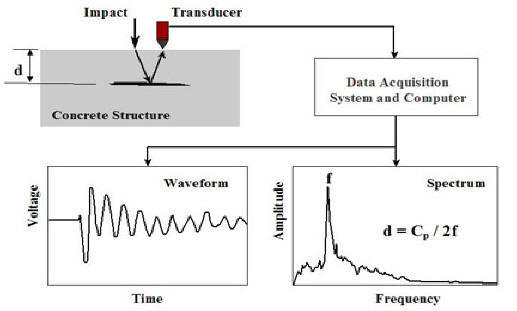
A short-duration mechanical impact, produced by tapping a small steel sphere against a concrete or masonry surface, produces low-frequency stress waves (up to about 80 kHz) that propagate into the structure and are reflected by flaws and/or external surfaces. The wavelengths of these stress waves are typically between 50mm and 2000mm — longer than the scale of natural inhomogeneous regions in concrete (aggregate, air bubbles, micro-cracks, etc.). As a result they are only weakly attenuated, and propagate through concrete almost as though it were a homogeneous elastic medium. Multiple reflections of these waves within the structure excite local modes of vibration, and the resulting surface displacements are recorded by a transducer located adjacent to the impact. The piezoelectric crystal in the transducer produces a voltage proportional to displacement, and the resulting voltage-time signal (called a waveform) is digitized and transferred to a computer, where it is transformed mathematically into a spectrum of amplitude vs. frequency. Both the waveform and spectrum are plotted on the computer screen. The dominant frequencies, which appear as peaks in the spectrum, are associated with multiple reflections of stress waves within the structure, or with flexural vibrations in thin or delaminated layers.
The fundamental equation of impact-echo is d = C/(2f), where d is the depth from which the stress waves are reflected (the depth of a flaw or the thickness of a solid structure), C is the wave speed, and f is the dominant frequency of the signal. The frequency f is obtained from the results of a test. To determine thickness or depth of a flaw, the wave speed C must be known. It can be measured by observing the travel time of a stress wave between two transducers held a fixed distance apart on the concrete surface or by performing a test on a solid slab of known thickness and observing the dominant frequency. In the latter case the equation is rearranged to give C = 2df (where d is the known thickness).
For an in-depth study of the technology, refer to the book written by the inventor of the method, Mary J. Sansalone.
View a list of technical papers by Dr. Sansalone and her co-workers (Impact Echo References PDF).